Working with the wind
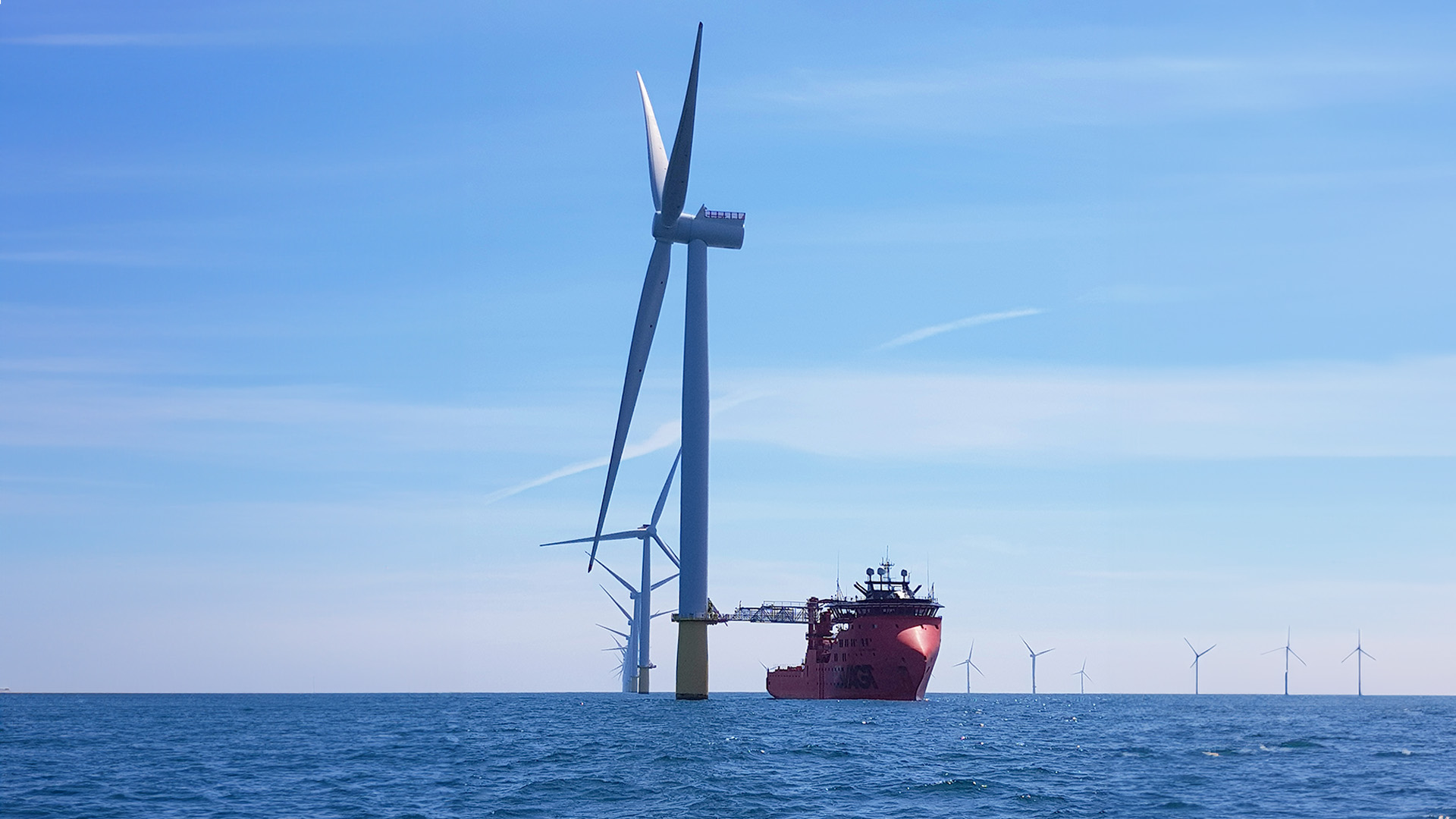
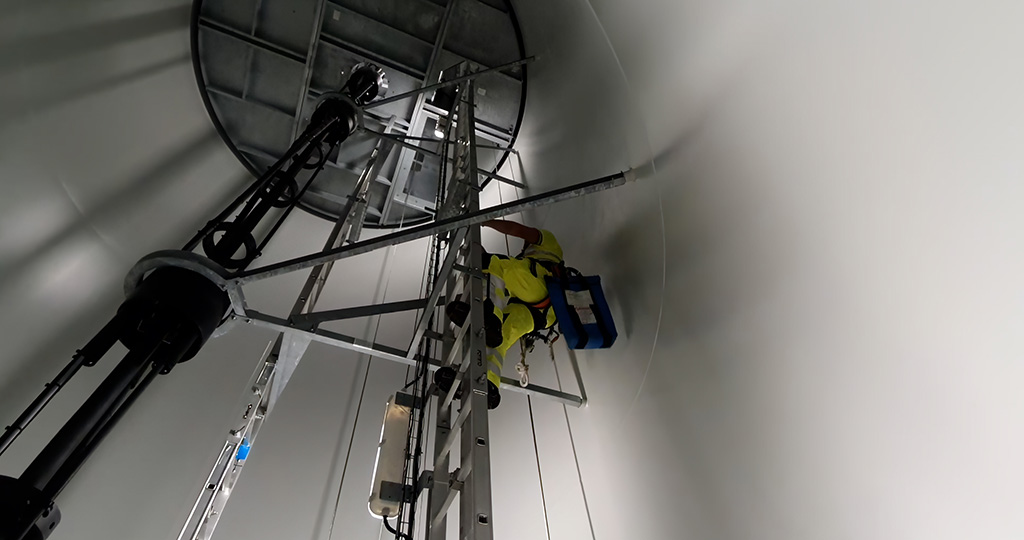
Off the coast of Norfolk in Britain, towering offshore wind turbines stand in orderly procession. A large team of technicians work every day to keep them in operation. This requires detailed logistical planning and a constant battle against the weather.
- Offshore wind
The UK's windy and relatively shallow shelf waters extend far into the North Sea and make the island nation one of the world’s key locations for the exploitation of offshore wind. Equinor operates the Dudgeon Offshore Wind Farm and Sheringham Shoal projects from its base in the small coastal town of Great Yarmouth.
The operations and maintenance base is staffed by engineers and a planning team who oversee the safe operation of the turbines. All work on the turbines out on the farms is coordinated from the base control room.
Watch video about how the base is operated
A total of 155 turbines are installed at these two wind farms. Each requires three to four days of annual maintenance to enable them to withstand the harsh weather conditions. This is in addition to repairs and upgrades.
“Our biggest challenge is organising the logistics of getting the technicians to and from their work”, says Colin Galer, Plant Manager at the Sheringham Shoal wind farm.
Why are we writing about offshore wind?
Regulatory responsibility for offshore wind power was delegated to the Norwegian Ocean Industry Authority (Havtil) in 2020. This authorises it to develop regulations for and conduct supervision of the development and operation of offshore wind farms.
A new regulatory framework for renewable energy production is now being prepared.
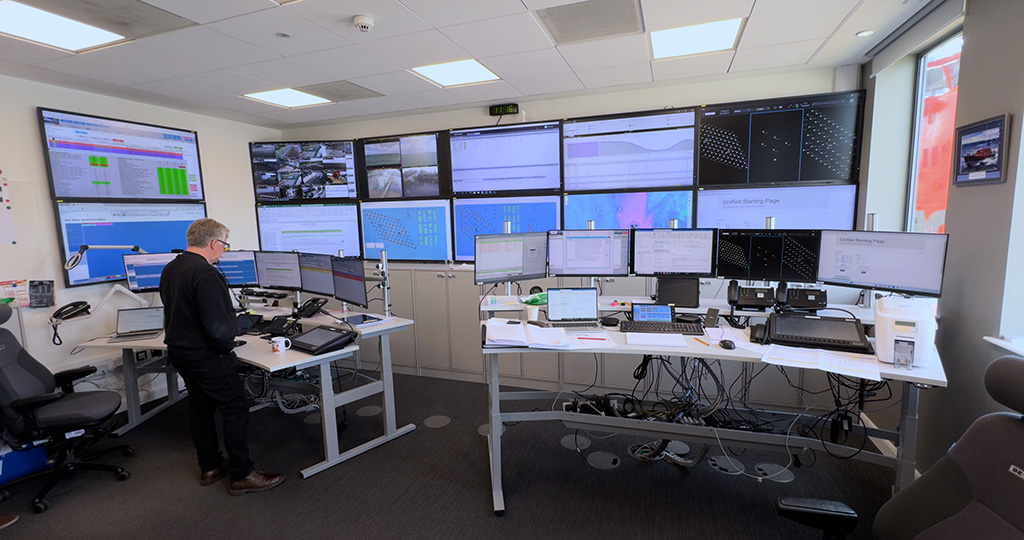
Challenging logistics
The technicians work two-week rotations offshore, based on the Esvagt Njord, a Service Operations Vessel (SOV) that has been custom-built for its task – serving as both a floating hotel and storage facility for component spares and equipment. Each day it transports technicians to and from their work on the turbines.
So many workplaces require significant levels of planning. What tasks are required on each turbine, and what equipment is needed for each task? What is the most efficient route to take? An emergency response requirement of 60 minutes for health personnel must also be taken into account.
With the exception of one day every fortnight for team rotation, work is carried out at the farms every day throughout the year – unless the weather puts a stop to things.
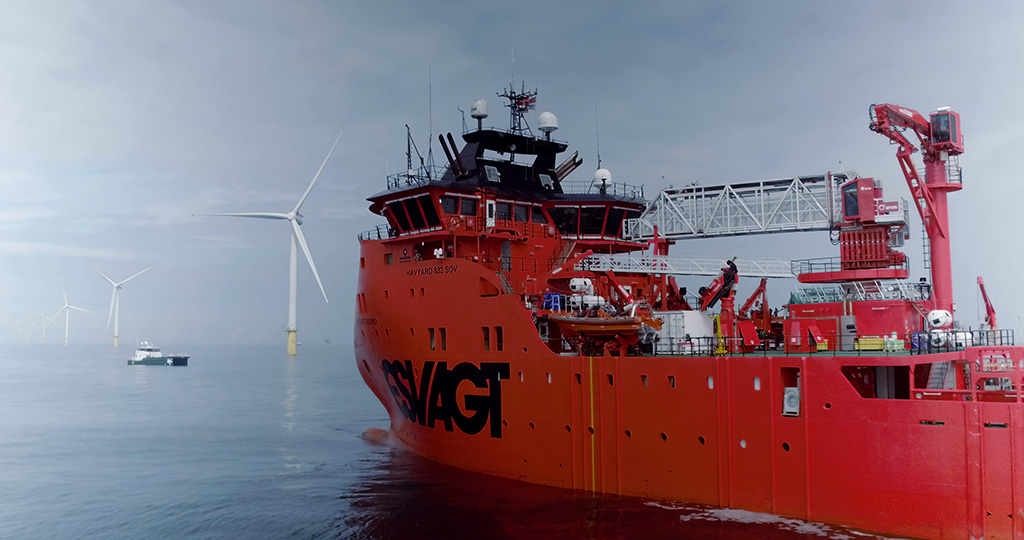
Hotel, taxi, warehouses and standby vessel
“Our main task is to ensure the safe operation of the wind farms”, says Stefan Sørensen, Master of the Esvagt Njord.
The permanent deployment of an SOV out on the farms is a new concept to the UK. The Dudgeon wind farm, located 32 kilometres out in the North Sea, is one of the wind farms furthest from land in the UK. The use of an SOV thus saves a lot of time that would otherwise be spent transporting technicians and equipment to and from the mainland every day.
Each morning, the Esvagt Njord carries technicians to their work on the turbines. The teams transfer from the vessel with the help of a specially-designed gangway – the so-called walk-to-work system.
“As the SOV approaches a turbine, an operator positions the gangway at a 90-degree angle. When the vessel is in position, he connects the walkway to the turbine and the technicians simply walk across”, says Sørensen. “This becomes challenging when we’re working close to limiting weather conditions and have to decide whether or not it is safe to send the technicians onto the turbines. Safety is my responsibility, but anyone on board is entitled to speak up if they don’t feel safe. Then we call a halt”, he says.
Technicians can also be transported to the turbines in small boats. These can speed around the wind farms faster than an SOV but require the technicians to step onto the turbine from the bow of the boat, which involves a 15-metre climb to reach the first landing. This is subject to a strict limiting weather threshold. While the ‘walk-to-work’ system is limited to wave heights of up to two and a half metres, the boat transfer operates with one and a half metres.
[Foto av walk to work]
Harsh weather
A working day for those out on the enormous offshore wind turbines is very different from that onshore. Two or three technicians will work on a single turbine for a whole day, exposed to the wind and rain.
“Our biggest challenge is the extreme and changeable weather conditions we encounter in the North Sea”, says the experienced technician Connar Delaney, who has been working at the Dudgeon facility for ten years, starting when he was only 18.
“Brilliant sunshine can change to high winds and rain in a very short time, so we have to be well prepared. We check the weather forecasts and choose the right clothing and safety equipment before we move out”, he says.
“But you never forget your lunch box! Once on a turbine, you have a long day ahead of you, so lunch is one of the most important things to remember”, he laughs.
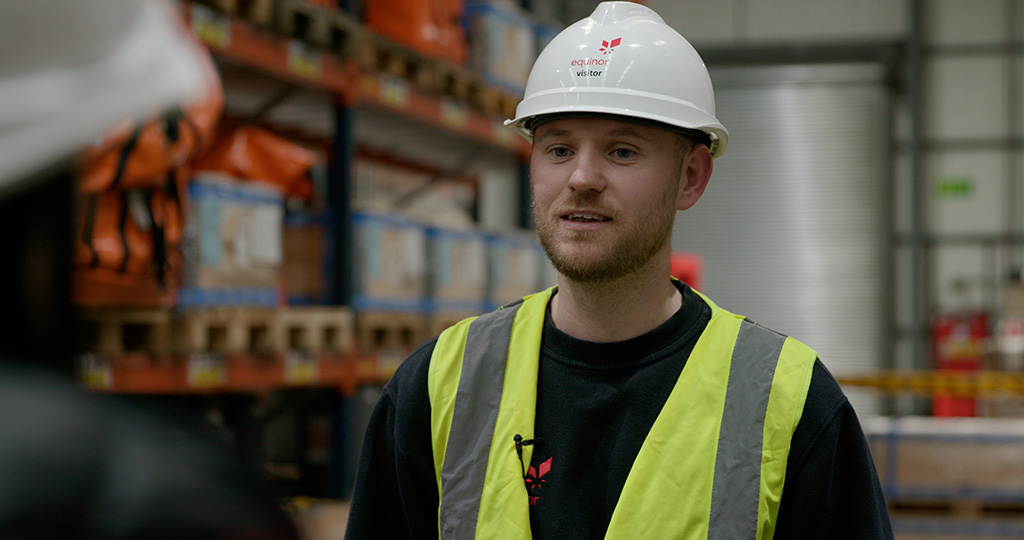
Once the technicians are on board the turbine and have taken the lift up to the nacelle, 100 metres above the sea, there are many demanding tasks that await them.
“As well as the climbing and the weather, the greatest risks are linked to crane operations and working with high voltages. But we’ve had extensive training and adhere to strict working procedures”, says Delaney.
In spite of these demanding conditions, Delaney feels very safe at work.
“We have harnesses, fall arrest equipment and permanent anchor points, so I feel safer out there than halfway up my house cleaning the windows”, he says.
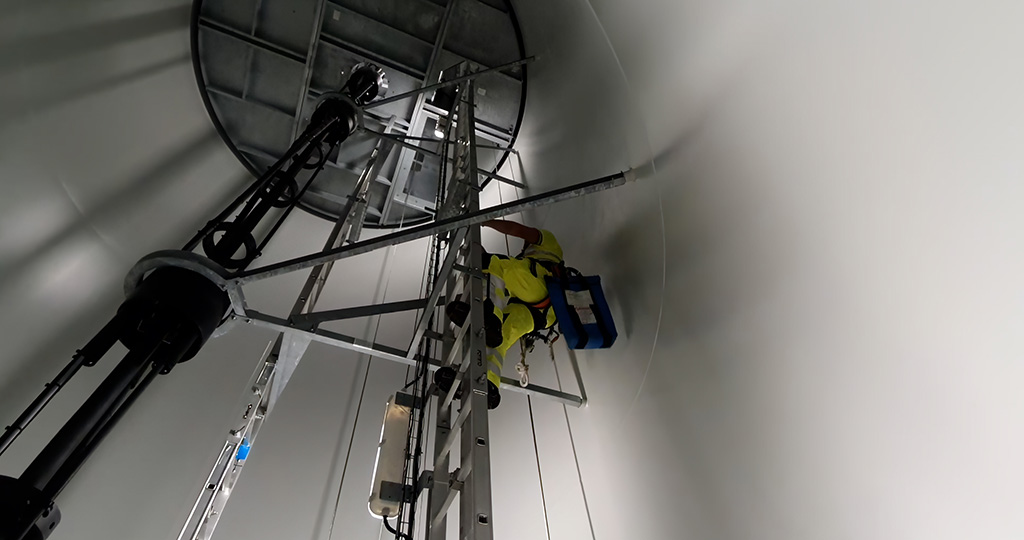
Lessons from the oil industry
Since hydrocarbons are not involved, the major accident risk picture for wind farms is somewhat different from that on oil installations. But they do share some common risks, such as those related to marine operations, fire, cranes and lifting operations and ergonomics.
“One of the main risks is the transfer of personnel from the vessels to the turbines”, says SSU Manager Luke Adams. “A technician's work also involves some climbing with heavy equipment, so there is a risk here of musculoskeletal issues”, he adds.
According to Adams, many years of experience in risk management in the oil industry is a great benefit when mitigating risk linked to wind farm operations.
“Among the most important lessons are the processes we use to identify risk. These are tried and tested, and we apply them both for risk identification and as the basis for our risk-mitigating measures”, he says.
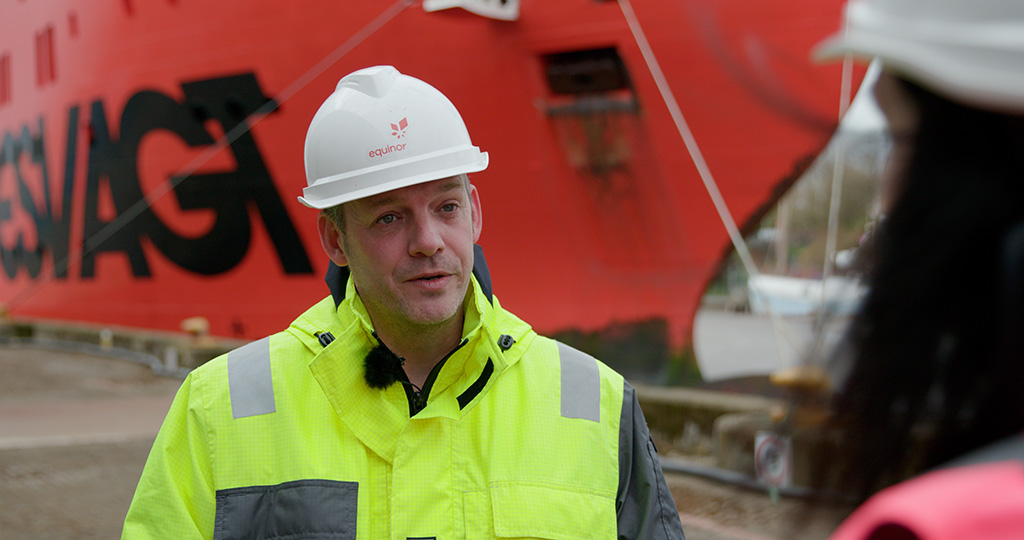
Expansion and extension
The Sheringham Shoal wind farm is now twelve years into its 20-year design lifetime, while Dudgeon is just eight years into a lifetime planned for between 20 and 25 years.
“We’re now starting to look into the potential and opportunities linked to extending these lifetimes”, says Galer. “Our future plans include expansions of both the Dudgeon and Sheringham wind farms that will double their production capacity”, he says.
Facts
Equinor’s base at Great Yarmouth serves as the operations centre for the Dudgeon and Sheringham wind farms, and the control room also monitors the Hywind Scotland project.
Dudgeon Wind Farm
- Location: 32 km offshore Cromer in Norfolk
- No. of turbines: 67
- Type: Bottom-fixed
- Installed capacity: 402 MW
- Supplies about 430,000 UK households
Sheringham Shoal Offshore Wind Farm
- Location: 23 km offshore Norfolk
- No. of turbines: 88
- Type: Bottom-fixed
- Installed capacity: 317 MW
- Supplies about 280,000 UK households
Hywind Scotland
- Location: 25 km offshore Peterhead in Scotland
- No. of turbines: 5
- Type: Floating
- Installed capacity: 30 MW
- Supplies about 20,000 UK households
Source: Equinor