Giant without compare
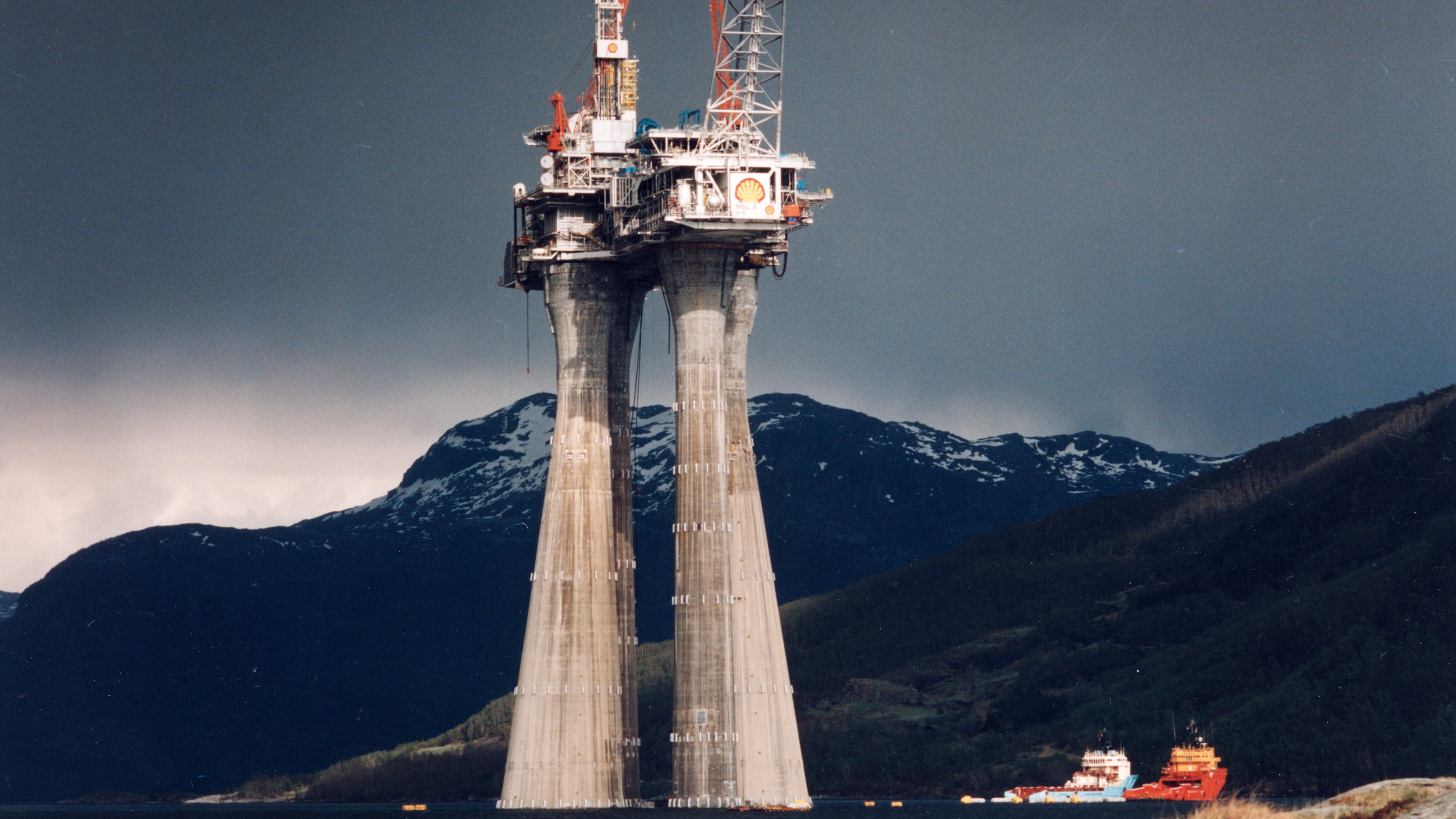
- Well integrity
- Structural safety
The small community of Vats north of Stavanger was witness in May 1995 to a sight nobody had seen before – the departure of the tallest structure ever moved by humans.
Towing the Troll A gas platform out to the North Sea was a source of astonishment and not least pride at Norwegian engineering skills.
“A wonder of the world, neither more nor less, was on its way down the Bokna Fjord,” says Bjørn Vidar Lerøen.
“But we can’t begin there, because there are so many dimensions involved.”
The former oil journalist, consultant and author knows Norway’s oil history well, and feels the need to sort through his memories before starting to talk about Troll.
This tale covers such aspects as geopolitics, technology development, engineering skills and exemplary resource management.
“May 1995 is definitely not the place to start,” explains Lerøen. “But Troll made its mark on the whole 1980s, in many areas.”
“Impossible” challenge
After well 31/2-1 in 1979 had proven what was to become the Troll field, it soon became clear that a thin layer of oil lay beneath the big gas reservoir.
That sparked a major technology hunt.
Both development operator Shell and production operator Statoil believed this crude was inaccessible and wanted to concentrate on the gas.
But the NPD, which had a dedicated team of specialists for the field, thought differently. And Norway’s Norsk Hydro company believed it had a solution for reaching the oil with the aid of horizontal drilling.
“Although this technique actually has a very long history, applying it in its traditional form wasn’t possible on Troll,” says Monica Ovesen, discipline leader for drilling and well technology at the PSA.
She explains that drilling horizontally has roots extending back to California in the 1930s, when people wanted to drive wells from land to reach oil deposits just off the coast.
They put wedges at a certain depth to function as a ramp for the drill string, Ovesen says. “Other methods were used, including ‘deviated’ wells, but they weren’t good enough for Troll.”
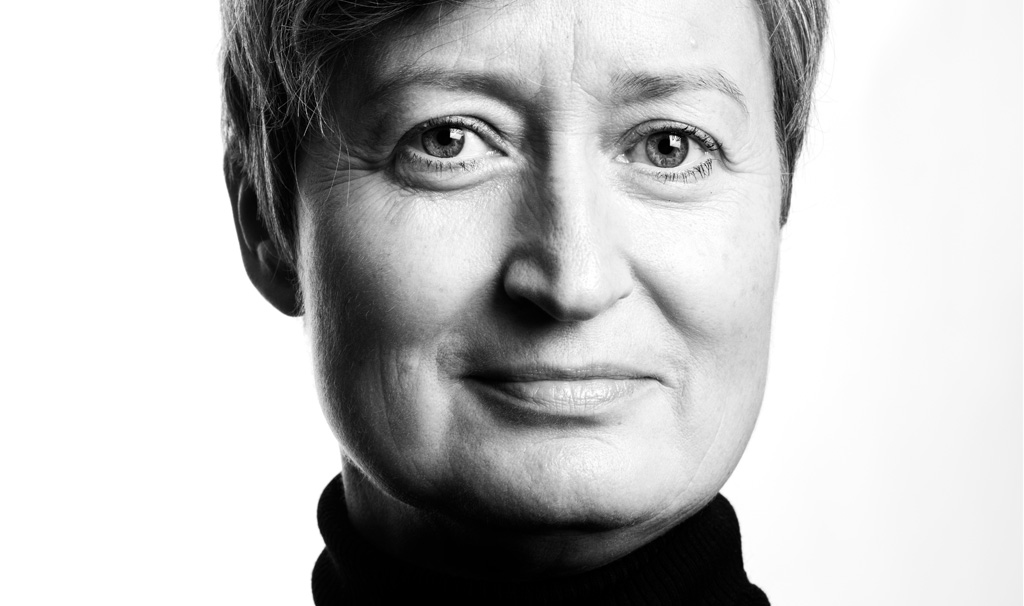
Safety challenges
Earlier versions of horizontal drilling provided insufficient control, and the 20-metre-thick oil zones under the Troll gas called for great precision in guiding the bit.
Extensive work between approval of the original PDO for Troll in 1986 until it came on stream in 1995 resulted in a rotating, continuously steerable system which is still in use.
“Put simply, this solution involves placing the sensors used for guidance as close to the bit as possible,” says Ovesen. “That reduces deviations and enhances precise control.”
Where the safety of drilling operations is concerned, this approach had both positive and negative aspects, she explains.
“There were fewer wells, and thereby less drill-floor work – a safety gain. At the same time, longer wells created issues related to downhole stability – a challenge for safety.”
Noting that complexity also increases, she says this is manageable in safety terms. The longest well on Troll is 10 042 metres, with a horizontal section of no less than 8 022 metres.
Extensive work between approval of the original PDO for Troll in 1986 until it came on stream in 1995 resulted in a rotating, continuously steerable system which is still in use.
Platform design
Troll was not only innovative and important for drilling. Work on platform design was a key feature throughout the 1980s, including when planning Troll A.
This was the first of three large facilities on the field, and a number of concepts were considered. They included a platform standing on the seabed and various floaters – known as “little trolls”.
But the ultimate choice was a Condeep – a fixed facility supported by a huge concrete gravity base structure (GBS). Nobody had proposed building anything like it before.
The dimensions were enormous. Various illustrations placed Troll A alongside such edifices as Oslo’s City Hall and the Eiffel Tower in Paris, but it loomed over both.
“Troll A was the equivalent to a Moon landing,” observes Lerøen.
Big fields first
But he points out that, amidst all the pride over technological and engineering achievements, an element of luck must be admitted in the story of both Troll and Norway’s oil sector.
“We were fortunate in finding the big fields early – Ekofisk, Statfjord, Snorre, Oseberg and Gullfaks. That’s been highly significant in many ways.”
In his view, the economic backbone provided by these discoveries, along with the experience gained from developing and operating them, was crucial for the technological achievements. “The financial power which the big fields gave us has also equipped the country for the future we’re now entering.”
But he emphasises that Norwegian oil history would have looked very different without the unique interaction between oil companies, suppliers, technology teams, government and unions.
“We had a generation of politicians and civil servants who saw the opportunities. And that naturally reflects another important element – the Norwegian temperament and mindset.
“Moreover, the administrative system provided orderly conditions and predictability. We can be proud of that as well.
“Norway also went against the flow. Most countries flared their associated gas, for example, but we decided to look after it all – a far-sighted decision we were almost alone in taking.”
US pressure
Troll gas attracted unexpected international attention in the 1980s. US president Ronald Reagan, concerned about America’s energy supplies, suddenly saw an opportunity on the NCS.
He thought the Troll gas could be important at a time when the Cold War was at its chilliest. Reagan feared that the world – and particularly Europe – would become too reliant on Soviet gas.
Troll could offer a chance to lessen that dependence. He accordingly argued three times in the US National Security Council that the field had to come on stream as soon as possible.
The Norwegians had to move faster, he asserted, and offered both cash and competence. “But Norway responded that it wanted to take time to develop Troll,” Lerøen observes,
And it did take time. Reagan did not get his way. The field was not in production before the mid-1990s, long after the Cold War was over.
“That’s a good example of Norwegian resource management,” says Lerøen.
“You shouldn’t go too fast, regardless of who’s applying pressure. Decisions must be properly grounded.”
Get the hard copy
Do you want to receive the special edition of "Dialogue" for free? Send an e-mail to dialog@ptil.no.
Parallels
Lerøen sees parallels with today’s position in the wake of Russia’s invasion of Ukraine and the significance of Norwegian gas for an EU which wants to become independent of Russian gas.
“That illustrates the important role of energy in international politics – for stability, peace and prosperity,” he emphasises.
“Troll has made its mark on Norway and the world in so many ways, and will continue to do so. When it was discovered, the field was expected to deliver gas for 70 years – a tremendous perspective.
Nobody knows whether this still holds good, because there are too many uncertain variables. But Troll’s significance for technology, economics and Norwegian pride will last far beyond this time frame.”
Milestones for safety in the 80s:
1980: Alexander L Kielland accident – 123 people dies. Follow-up of the accident prompts extensive changes to the existing organisation of regulatory responsibility for HSE.
1985: Storting passes the Petroleum Act. NPD receives lead responsibility on developing regulations for and supervising safety and the working environment in the petroleum sector (both fixed and mobile facilities).
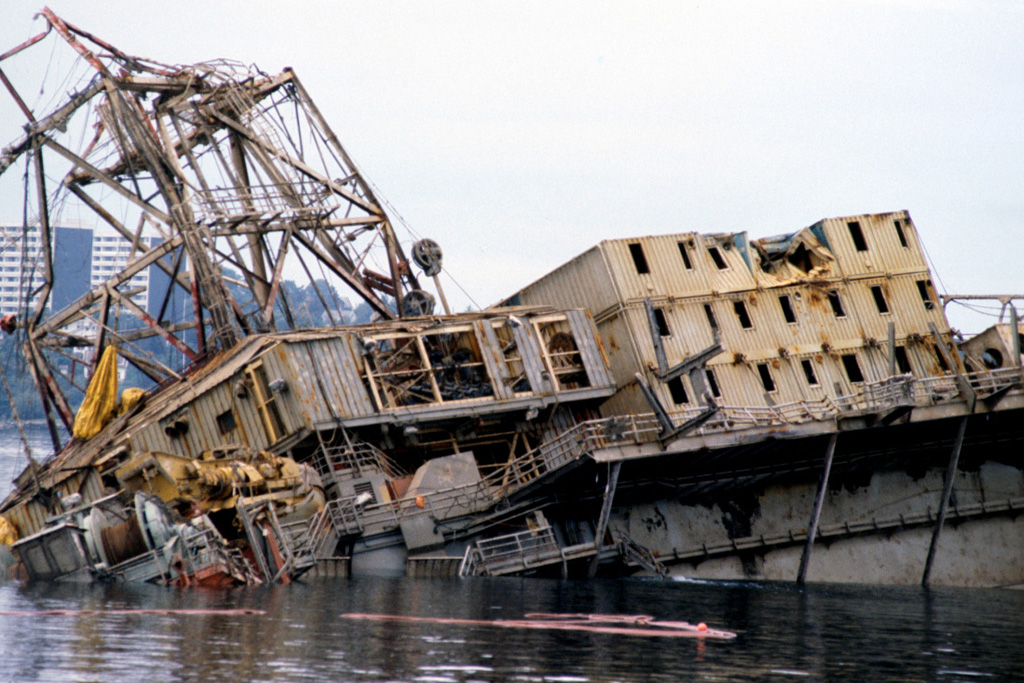
Concrete controversy
One of the very first big concrete Condeeps on the NCS was Statfjord A. After a number of modifications, the NPD’s safety division decided this design was sufficiently secure and gave the green light for construction in 1976.
Following many further adjustments and changes, the facility was ready to come on stream in 1979. Operator Mobil proposed a straight copy of Statfjord A for the second platform.
The NPD then put its foot down, and rejected the project on the basis of an overall safety assessment. In a response later dubbed “the most expensive letter in Norwegian history”, it demanded that the living quarters be placed on another platform.
After many meetings and long discussions, Mobil produced a new layout for the topsides on Statfjord B to improve separation of the quarters from areas where fire or explosion could occur.
The same concept also formed the basis for the Statfjord C facility and the three Condeeps on Gullfaks.
This approach to managing safety by building in prudent solutions at the planning phase was eventually extended to cover a number of other types of risks.
Understanding the Norwegian regime
The Norwegian model for managing safety in the petroleum sector may seem complicated. We have sought to produce an educational guide to the safety regime.