Learning difficulties
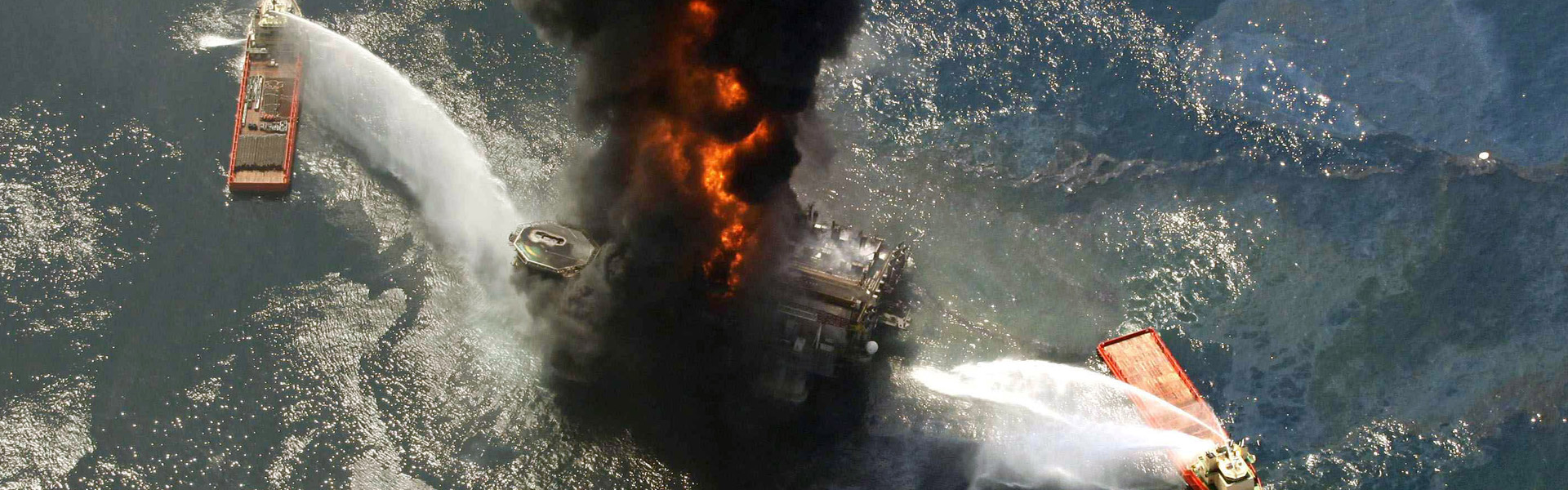
Safety specialist Ranveig Kviseth Tinmannsvik thinks the oil companies learn too little from serious incidents. “We’re fairly good at investigating, but fall short in applying the lessons,” she says.
- Risk management
Both the companies and the government devote substantial efforts to investigating serious incidents in the petroleum sector. But failure to learn from the findings is a recurring theme.
The question is then whether sufficient benefit is being gained from the commitment to conduct such investigations. Is the industry drawing the necessary lessons?
A senior researcher at the Sintef foundation, Ranveig Kviseth Tinmannsvik has studied learning from incidents for many years. She emphasises that much good and systematic investigatory work is done by the companies.
In her view, however, the weak point lies in the follow-up, with the systematic approach and attention seen in the inquiry missing once it has been completed.
“An investigation can obviously identify important direct and underlying causes of an incident, but drawing lessons from this calls for much more,” she emphasises.
Changes
“The ideal learning process yields specific changes in technology, equipment, procedures and behaviour. The organisation also becomes more conscious of its ability to learn from incidents.”
Tinmannsvik points out that disseminating information in the wake of an accident or the like is not enough to ensure that the lessons are learnt.
“Sharing information is easy. The question is whether the recipient has the capability to convert it into specific measures tailored to local conditions in their own organisation.
“It’s important to decide who should be involved in adopting measures, what requirements should be set for them, and how we’re going to measure their effect.”
Raised
She wants to see more ambitious targets set for learning. Noting the frequent claim that an incident must be investigated to prevent repetition, she says that this goal is far too modest.
“If we conduct a thorough investigation by seeking out the underlying causes, we’ll prevent not only similar events recurring but also other types of incidents and accidents happening at all.
“So the aim must be learn more than simply stopping the same type of accident happening again.”
Demanding
Investigation is a precondition for learning. But the most demanding work comes afterwards, when the findings are to be converted into measures and follow-up.
“Good decision processes for selecting and implementing measures are crucial in learning lessons,” Tinmannsvik observes. “Our starting point here is often a little too narrow.”
She urges the industry to concentrate less on individual incidents when deciding on measures, and to look instead at the overall risk picture.
“It should draw on several information sources, including results from other investigations, risk analyses, and internal and external audits.
“Finding out what concerns the employees have in their day-to-day work is not least important. What subjects are raised at HSE meetings in the companies, for example?”
Prioritise
Tinmannsvik emphasises the significance of daring to prioritise: “Choose a few long-term improvements rather than a lot of short-term correctives.
“Pursuing too many measures at once will undermine concentration and the motivation for making changes. If everything’s important, nothing is.”
She believes that the measures given priority must be followed up in detail, and stresses that failing to assess their effect means an amputated learning process.
“We see that companies often sign off measures with a starting point in an intention or a plan to adopt them, rather than waiting until they are actually implemented and assessing their effect.
“If we let go of the measures too early, before they’re put into effect and their outcome is evaluated, learning opportunities will be lost. So it’s important to see this work through and follow it up over time.”
Dialogue article
This article has been taken from our Dialogue journal, which aims to encourage debate on some of the most relevant issues and challenges faced by the industry in the safety area.