Five decades of getting better
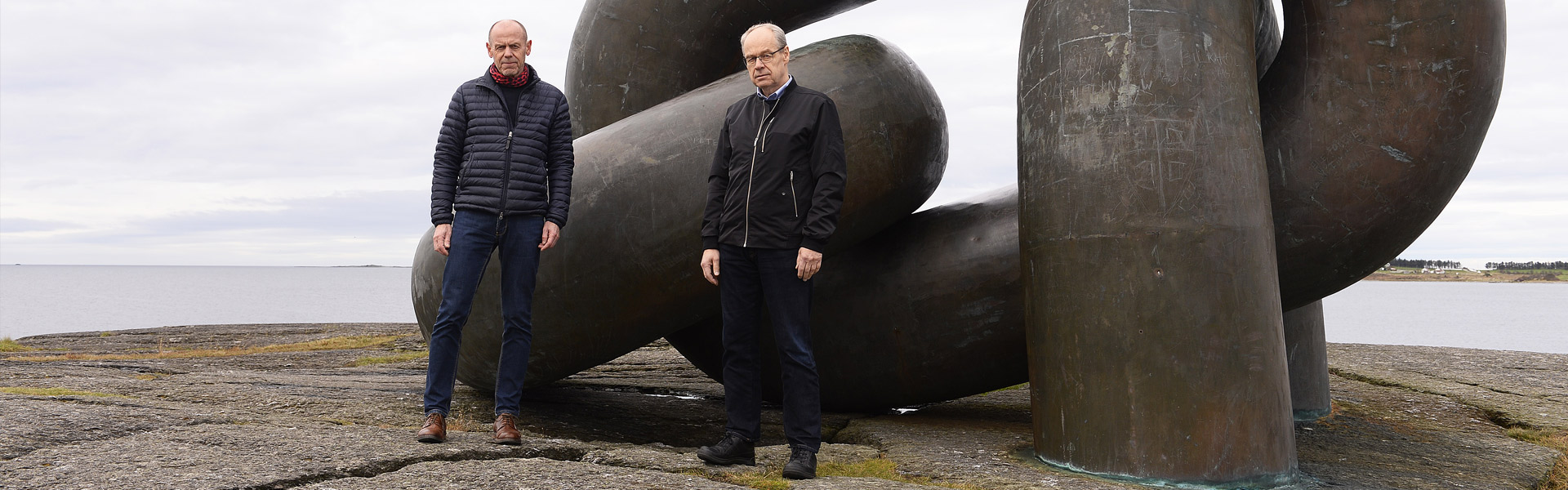
When Norway’s offshore “grand old lady” reaches 50, attention naturally concentrates on the value and prosperity it has created. But the Ekofisk story also includes important steps towards the present level of safety for the whole Norwegian oil sector.
- Structural safety
- Emergency preparedness
- Risk management
A number of accidents and serious incidents occurred during the first decades of petroleum operations on the Norwegian continental shelf (NCS), and the Ekofisk area was hard hit.
Occurrences there included several helicopter crashes, a fire on the Ekofisk 2/4 A platform in 1975, with three deaths during the evacuation, and the major Bravo blowout two years later.
Then came the Alexander L Kielland disaster in 1980, when 123 people lost their lives. All these incidents are part of Norway’s oil history.
“It’s important that we don’t beautify the story of Ekofisk, because it’s had a cost,” says Stig S Kvendseth, head of communication and government affairs at operator ConocoPhillips.
“Phillips was the operator when Kielland capsized, and that accident left deep traces in the company. When I joined [the following year], it hung over everything.
“It made a strong impression. Everyone was affected by what had happened, which left them both humbled and determined to learn the lessons.”
Influenced
“When we look back, it’s easy to see how accidents have influenced progress with safety and the regulations,” says Bjørn Saxvik, who has been with ConocoPhillips since 1984 and is now HSE manager for the Ekofisk area.
“During the early years, unfortunately, it was the accidents which prompted the big advances in this area. New solutions were found after things had happened.”
He points to several examples of this, such as the Bravo blowout. That led to Norway’s oil spill response system and the Norwegian Clean Seas Association for Operating Companies (Nofo).
Helicopter accidents made wearing survival suits obligatory on flights. And Kielland prompted changes in training, protective equipment, rescue gear and regulations as well as mandatory risk analyses.
“Things are different today,” Saxvik acknowledges. “Over the years, we’ve become much better at looking ahead, calculating what might happen and taken action on the basis of potentials.
“This approach has helped to ensure that it’s a long time since we had a major accident. The goal today is zero accidents in the industry.
“That’s done something with our mindset. We’re more proactive, always in the forefront and work very differently from before. It’s important not to lag behind in the safety sphere.
“Analyses initially focused primarily on technology, but the human and organisational aspects have secured a stronger place over time. Their interactions are more and more important.”
Read more: Ekofisk: Safeguarding the heritage
Injured
Occupational injuries were not unusual for oil workers once. But Kvendseth says the image of dirty overalls on the drill floor and hands missing two fingers is a long way from today’s reality.
“Automation and new technology have meant that many of the jobs which called for manual work with a big exposure to risk are now gone.
“One example is the drill floor, where we’ve gone from manual handling of heavy equipment in constant motion to a high degree of automation. You can now sit in a chair and operate remotely.”
He also cites remotely operated subsea vehicles and drones as examples of the way technological progress has helped to reduce risk exposure for personnel.
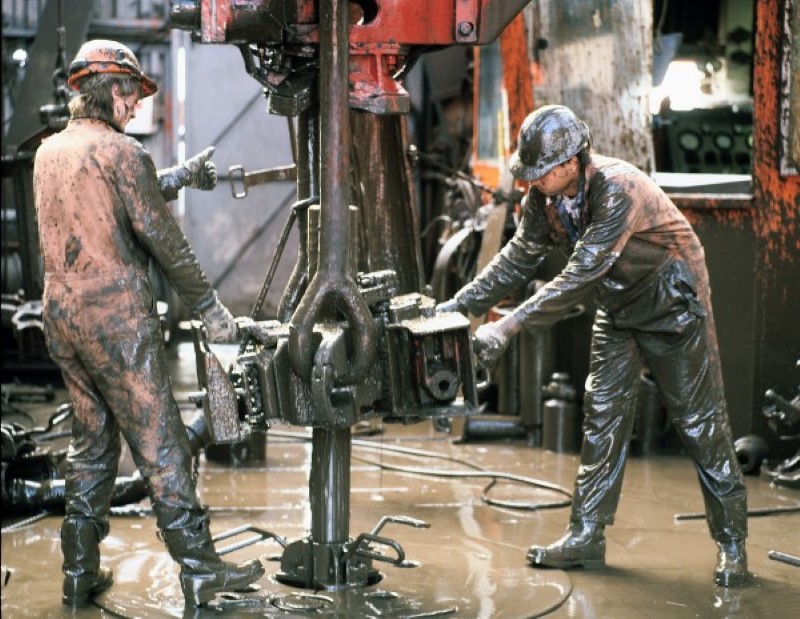
Challenge
The risk level on the NCS is very different today from the 1960s and 1970s. But that will only last as long as it is maintained. The challenge is to ensure that people are always alert and aware.
“Highlighting earlier incidents and accidents is important for maintaining attentiveness,” observes Saxvik. “We have to learn from the mistakes of others and what’s happening around us - in other oil companies and other industries.”
He believes that the exchange of experience between the companies on the NCS functions well today.
Awareness
“The companies don’t compete with each other over HSE,” Saxvik says. “On the contrary, I think there’s an awareness that we stand together on this.
“If a major accident occurs, we’ll be condemned as an industry and not just as an individual company. So it’s important that we constantly learn from each other.
“As a licensee, too, this company’s very active in safety work. We’ve found that our safety mindset is one of our biggest ‘exports’ to other companies.”
Kvendseth notes that ConocoPhillips has achieved good safety results over many years: “At the same time, we’re very respectful about this. We know that safety’s a perishable commodity.”
He believes that long-standing collaboration and trust between unions and management in his company has been an important factor in achieving good results.
“We have the room to talk together about the things we disagree on. Safety has a lot to do with the culture which prevails in the workplace.”
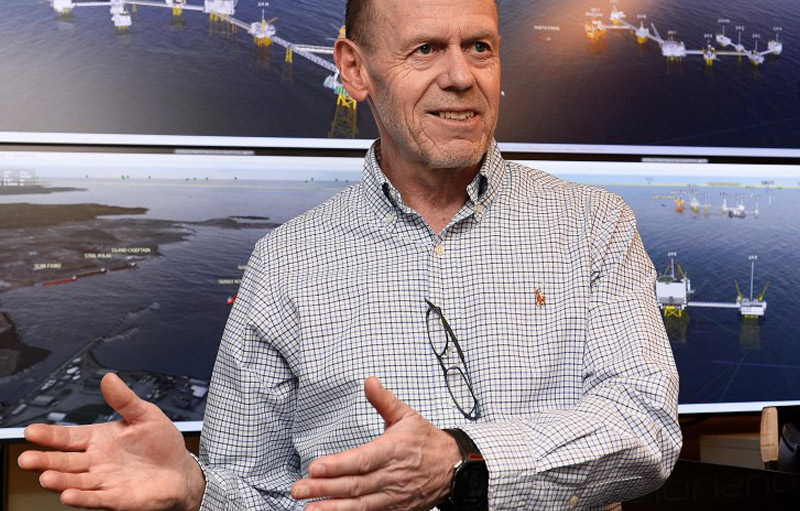
Available
When Ekofisk was developed, the companies drew on the knowledge and experience then available. Much of this came from the Gulf of Mexico, where the waters were both calmer and shallower.
“Conditions in the North Sea were tough,” says Kvendseth. “The Americans encountered a quite different reality there, and had to go through a demanding learning process.
“But that resulted in a technological and safety progress which has been very important for activity both on the NCS and internationally.”
Since trial production from Ekofisk began in 1971 and up to 2019, the field has yielded 4.2 billion barrels of oil equivalent – and six billion in all from the greater Ekofisk area.
Some 180 000 barrels a day are still being produced, and the field is set to remain on stream at least until 2050.
“Tailoring safety work to technological advances will be an important job for the future,” Kvendseth notes. “We must always try to understand the interaction between technology and people.
“Good collaboration with our employees and our suppliers occupies a key place. And, not least, we must constantly learn from others.”
Dialogue article
This article has been taken from our Dialogue journal, which aims to encourage debate on some of the most relevant issues and challenges faced by the industry in the safety area.