Opinion: The small major incidents
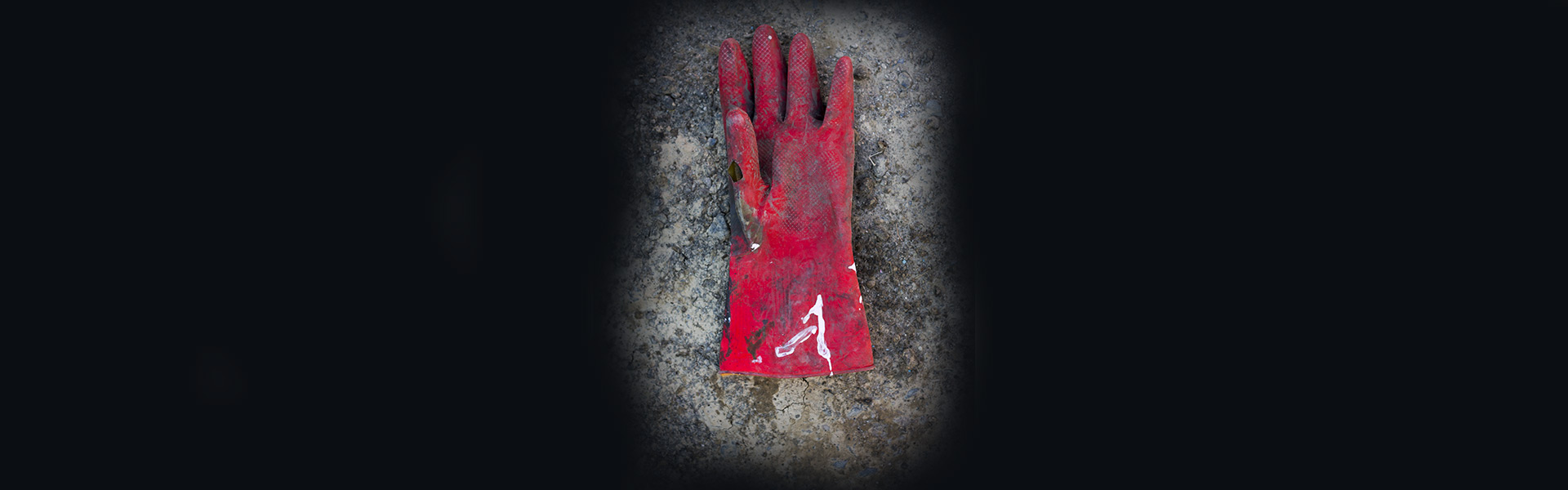
Within the space of a few months, Norway’s oil industry had moved from optimism to gloom. Big downsizings are being reported daily. Warnings have been issued from many quarters that reducing maintenance and operational staffing will weaken safety work and strengthen the risk of a major accident.
A major accident is defined as an acute incident, such as a major discharge/emission or a fire/explosion, which immediately or subsequently causes several serious injuries and/or loss of human life, serious harm to the environment and/or loss of substantial material assets.
Fears that cost cuts could increase the risk of a major accident are genuine, and have to be treated with the utmost seriousness.
But it must also not be forgotten that periods of retrenchment can severely affect spending to improve the working environment and reduce the risk of health damage. Lost time caused by accidents is tiny compared with absences and losses attributable to physical strain, noise and exposure to chemicals.
Tougher
All the crisis reports about downsizing fuel fears of a tougher working environment. The consequences for somebody who can no longer cope with their job will be a poorer quality of life and financial problems.
That can unquestionably be called a major incident at a personal level. So it is important to remind each other of the big effect and loss which an individual could suffer if the working environment becomes a balancing item.
People on most offshore platforms are greeted with statements such as “the goal is that you will be just as healthy when you go home as when you arrived”. Good injury statistics are generally cite. Unfortunately, few data exist on the harm done by a poor working environment.
In an era of cost cutting, savings are sought across the board. Among of the first things to go are time for courses and training. Full-time posts for safety delegates are withdrawn, and the time allowed them to do safety work reduced. We also see a reduction in professional personnel working on HSE.
Damage
The petroleum industry handles countless chemical compounds and products which can harm health. They include substances which can cause brain damage and affect memory and mental state through long exposure.
Other compounds may reduce lung function over time or produce allergic reactions in the respiratory system or on the skin. Such damage occurs gradually. Chemical exposure is seldom so acute that the harm done shows up in the injury statistics.
Many jobs in the petroleum industry must be performed with the use of personal protective equipment (PPE), such as respirators, chemical-resistant gloves and overalls. Using the right PPE is particularly critical for people involved in surface treatment.
Many companies find such products to be a substantial cost item. Poor operating parameters do not make the position any easier.
Competition among insulation, scaffolding and surface treatment (ISS) contractors is tough, and jobs go to the lowest bidder. Few resources are allocated to training, while personnel are urged to save on the use of PPE – a dangerous combination which can quickly lead to even more serious health problems.
The ISS trades fall into the category of groups particularly exposed to the risk of occupational injury and illness. Changes to the better for these workers are unlikely until those who want the jobs done specify tools, training requirements and PPE in such a way that the successful bidder is the one with the best system for quality and HSE.
Occupational ill health caused by exposure to chemicals often provides little opportunity for redeployment to alternative work. And it is very difficult to get such injuries approved for compensation or disability pensions.
Those affected must not only contend with poor health but may often also end up in financial difficulties. Loss of health, job and income by a breadwinner is a major incident, which affects their whole family.
Ability to hear
Most of us can readily grasp that losing the ability to hear nature’s sounds, converse easily or enjoy music represents a big loss.
A high noise level causes such damage as hearing loss and tinnitus. Deafness can be so serious that it becomes difficult to converse in a room with several people present. That often leads to misunderstandings and social isolation at work.
Those affected suffer considerable loss. Some must quit because they can no longer function in the workplace. Many have problems with their social life.
Tinnitus is a persistent noise in the ear, often called “the devil’s orchestra”. Sufferers get no peace and can no longer enjoy silence. The condition ruins sleep and the ability to concentrate, and can turn those with it into invalids.
Noise-reducing measures and the use of quieter equipment could well be one of the areas where the industry makes cutbacks. In these circumstances, it is important to remember that hearing damage is not just something which afflicts a few per cent of the workforce, but also directly affects an individual – and in a tough and brutal fashion.
We have been through several years of very high activity in the petroleum sector. Many good working environment measures have been postponed through a lack of capacity.
My hope is that those wielding the savings axe can ask themselves the simple question: would I have subjected myself to what I’m asking my workforce to accept? Perhaps some deep reflection about the consequences of a poor working environment would provide the answer.
We now have both the capacity and expertise available. Let us implement the good preventive working environment measures.
Halvor Erikstein is an occupational hygienist and organisation secretary in the Norwegian Union of Energy Workers (Safe). He is also a member of the Safety Forum, the Petroleum Sector Board, the professional council of the Norwegian Occupational Hygiene Association, and the board of Global Cabin Air Quality Executive. He has been a member of the management committee for the petroleum industry’s chemical and noise project.