Shifting to the seabed
Underwater technology occupies a key place in the conquest of the NCS. Progress in this area really picked up speed in the 1990s, and Norway ranks today as a leading exporter of subsea solutions.
- Structural safety
- Process safety
The move to the seabed became the key to continued development of the NCS after the first large fields were brought on stream in the 1970s and 1980s.
Discoveries previously considered non-commercial became accessible with the aid of subsea solutions. More than half the petroleum produced on the NCS today comes from seabed wells.
“This technology made it possible to reach waters too deep for fixed steel and concrete installations,” says senior researcher Kristin Øye Gjerde at the Norwegian Petroleum Museum.
“It also became feasible to extend a network of seabed wells across a large area and thereby increase recovery from fields with complex reservoirs.”
With Arnfinn Nergaard, Gjerde has written Getting down to it. 50 years of subsea success in Norway, on how the country became one of the world’s leading exporters of underwater technology.
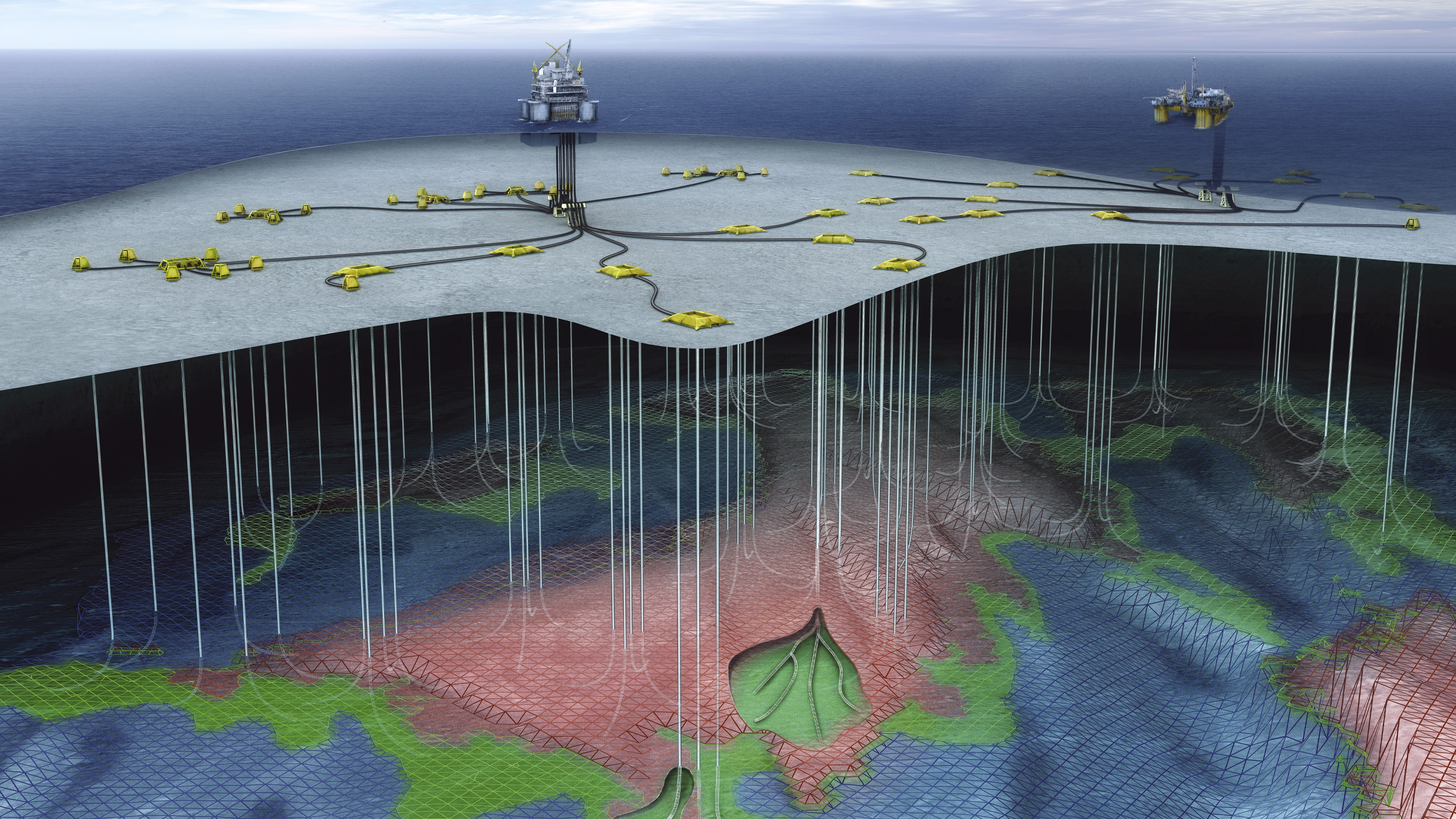
Solutions and standards
Activity in the Norwegian petroleum sector during the early 1990s was characterised by low oil prices, high costs and great uncertainty about the resource base.
However, the use of seabed wells on Frigg, Gullfaks and Tommeliten during the 1980s had shown that it was possible to produce from subsea installations.
That opened the way to using advanced underwater solutions for developing many discoveries previously regarded as unprofitable or inaccessible.
A big oil-price slump in 1986 had made finding cost-efficient approaches important. Field developments in the 1990s were driven by two opposing requirements.
On one hand, new technology was essential for overcoming such challenges as piping unprocessed wellstreams over long distances. On the other, standardising existing methods would help cut costs.
“The 1980s was about developing and adopting new solutions,” says Gjerde.
“In the next decade, the companies began to ask whether things could be simplified by re-using these innovations.”
She explains that the breakthrough came with the subsea wells tied back to Draugen and the Statfjord satellites, which were being developed more or less simultaneously.
“Norway’s Kongsberg Offshore came up with the idea of supplying virtually identical equipment on both fields, which sharply reduced costs. That marked the start of what became mass production of modularised subsea facilities.”
The new seabed modules were quicker to produce and simpler to install, making them more cost-effective than platform-based concepts.
This coincided with the launch of the Norsok project in the early 1990s, which aimed to reduce execution time and costs for building and operating facilities on the NCS.
An important part of this effort involved developing a number of Norwegian standards for the subsea area. Since few international equivalents existed, the bulk of these were adopted by the International Organisation for Standardisation (ISO) in the 2000s.
Milestones for safety in the 90s:
1992: NPD introduces regulations for mechanised pipehandling on the drill floor, after much conflict.
1992: WEA also extended to mobile units.
1993: Norsok project launched. Important industry collaboration on industrial standards.
1999: RNNP tool established. First annual report issued in 2001.
Floaters
A key feature of the 1990s was that subsea wells largely came to be tied back to floating platforms or production ships. Åsgard, on stream from 1999, was the biggest field developed in this way – with three floaters and more than 50 seabed wells.
Nine large subsea developments tied back to floating units were implemented in 1995-2001, and such tie-ins were used for more than half of all new seabed wells on the NCS in the 1990s.
“In reality, the arrival of the floaters put the nail in the coffin for concrete platforms,” observes Gjerde.
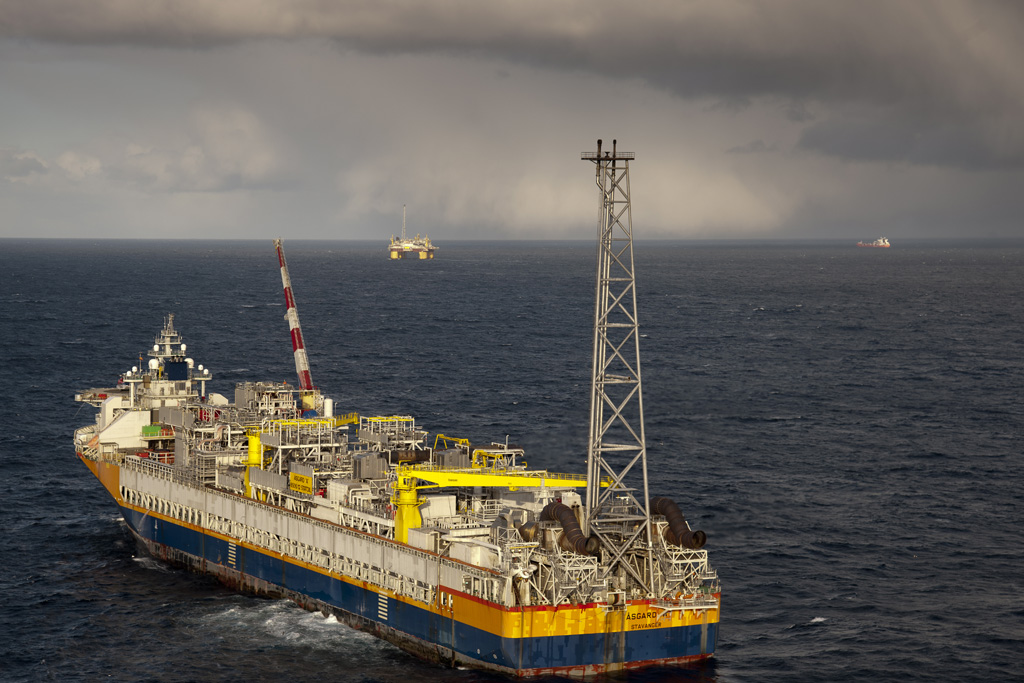
Subsea to shore
Important technological advances in the 1990s also made it possible to tie subsea wells directly to processing facilities on land.
Scientists at the Institute for Energy Technology (IFE), Sintef and the Norwegian University of Science and Technology (NTNU), took a key step forward with multiphase flow in pipelines.
This allowed unprocessed wellstreams – a mix of oil, water and gas – to be piped more easily over long distances, and again helped to make non-commercial finds relevant for development.
One example is Snøhvit in the Barents Sea. First discovered in 1984, it was not brought on stream until 2007 when long-distance pipeline transport of its gas became feasible.
Thanks to multiphase flow technology, gas and condensate can be piped 143 kilometres from this field to the Hammerfest LNG plant on the north Norwegian coast.
Subsea factories
Technology developed in the 1990s laid the basis for big breakthroughs which were to become important in the following decades, such as subsea compression and separation.
Both these solutions are key components in the concept of a “subsea factory”, and making this a reality became an important target for Statoil in the 2010s.
“After oil prices fell in 2014, there was less talk that everything had to be done on the seabed,” Gjerde notes. “Instead, the companies picked the best from every world.
“If the water depth is shallow enough, a fixed steel platform might be the best answer. Elsewhere, a floater could prove more appropriate.”
World leader
Technological progress in this period also provided a basis for export sales, making it possible for Norwegian companies to get established almost everywhere with production offshore.
That has particularly meant a lot for the supplier industry. Subsea technology ranks today as one of Norway’s largest export sectors, on a par with foreign sales of fish.
Gjerde is convinced that subsea expertise will also be important in the future:
“It’s highly relevant for floating wind power, aquaculture and possible recovery of seabed minerals.”
Get the hard copy
Do you want to receive the special edition of "Dialogue" for free? Send an e-mail to dialog@ptil.no.
Same safety demands
“From the perspective of personnel safety, subsea facilities represent a good answer because no people are present,” says principal engineer Trond Sundby at the PSA.
Safety work in this area therefore concentrates primarily on preventing leaks to the sea, he explains, and emphasises that the regulatory demands are the same as for surface installations.
“The requirements for double barriers and that a facility must default to a safe condition if a fault occurs also apply subsea,” he notes.
Figures from the section of the RNNP (RNNP AU) tool on acute emissions show that few leaks have occurred from seabed facilities and pipelines.
“The industry must nevertheless do more in this area,” Sundby says. “As more and more equipment and processes are placed on the seabed, the need for management and control increases.
“That in turn makes bigger demands on instrumentation and reliability. It’s important the companies understand this, and continue working to develop norms and standardised solutions.”
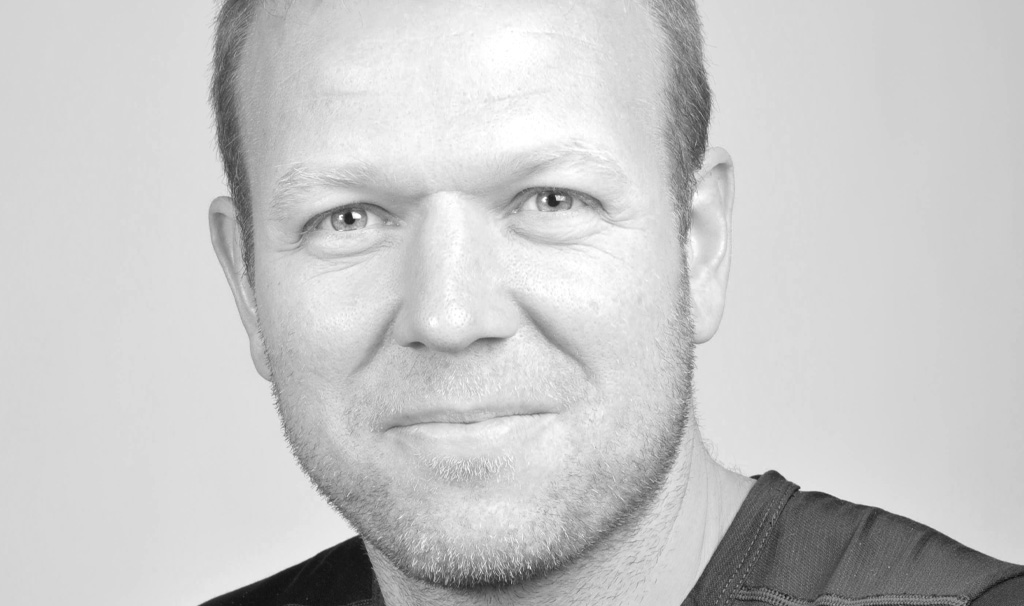
Good resource utilisation
Like Gjerde, he emphasises that subsea technology is also relevant for new offshore activities.
“The industry has been able to think long-term and in a solution-oriented way.
“If it manages to remain just as forward-looking in terms of technology development and standardisation as it was in the 1990s, steady subsea improvements will be possible. And that’ll be useful for offshore wind power facilities, for instance.”
Sundby believes underwater solutions will be an important part of the petroleum industry for many years to come.
“This technology has proved crucial for recovering more of the resources. Even more new oil and gas discoveries will therefore be tied back to existing facilities using subsea methods.”
As more and more equipment and processes are placed on the seabed, the need for management and control increases. That in turn makes bigger demands on instrumentation and reliability. It’s important the companies understand this, and continue working to develop norms and standardised solutions.
Capacity and expertise
At the same time, concern is growing that the expertise might wither. Many capable specialists at the subsea suppliers were lost during the 2014 downturn.
The industry is also currently experiencing a change of generations, with many of those who were involved in building up the sector now taking retirement.
“We have very able suppliers in Norway,” says Sundby. “The threat is that we’ll lose both history and knowledge. That’s a challenge.
“Expertise in the industry is important both for the petroleum sector and for new ocean activities such as offshore wind power.”