When the NCS became Norwegian
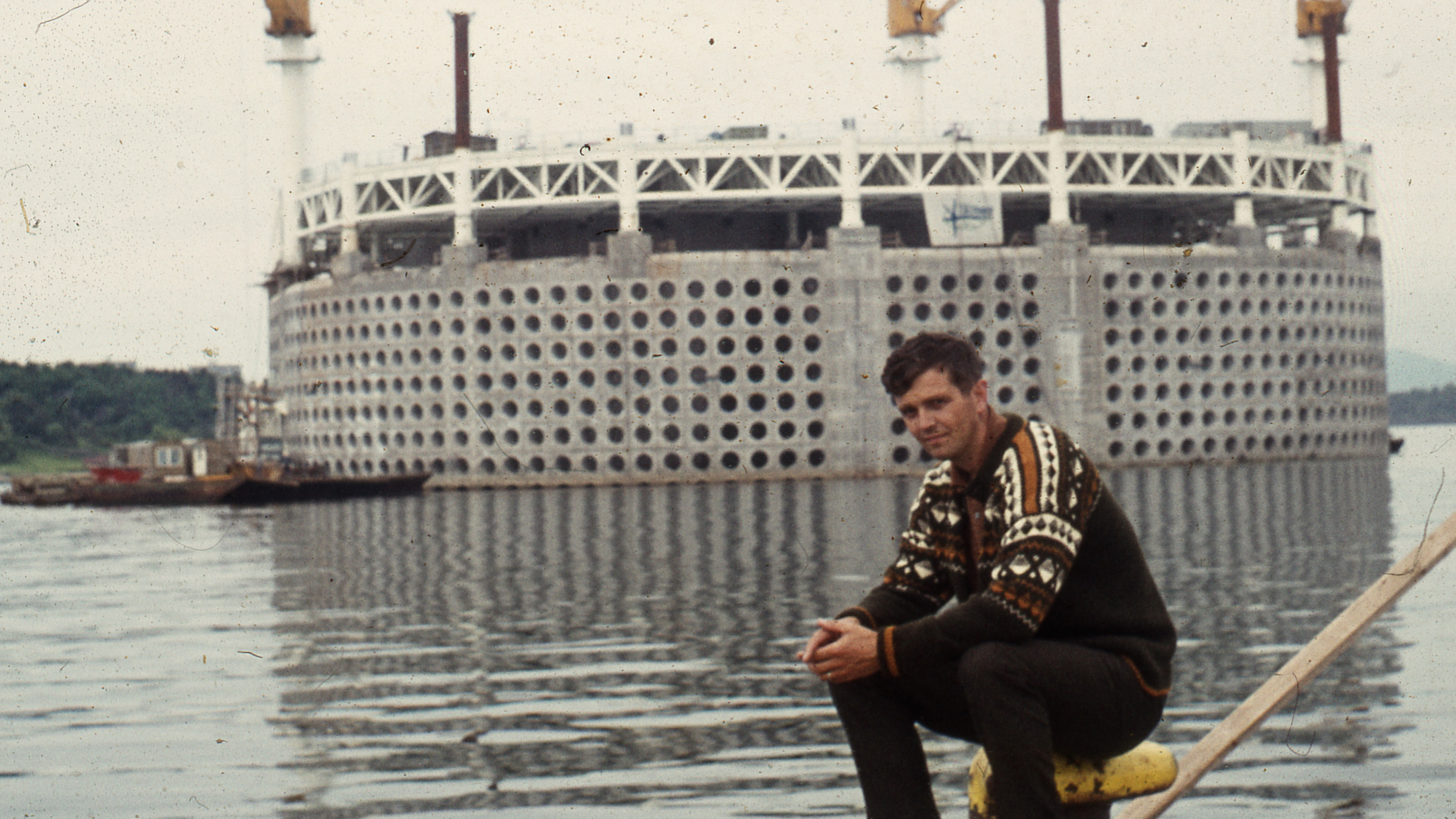
- Working environment
- Process safety
The number of accidents in the petroleum sector was high during the 1970s, which eventually attracted great public attention focused on NCS working conditions.
Another incident occurred on 1 November 1975 when a riser on Ekofisk Alpha caught fire. The platform was evacuated, but three crew died because a rescue capsule fell during lowering.
Turning point
That accident proved a turning point in securing a greater commitment to safety on the NCS.
“The fire on 2/4 A led directly to the establishment of the safety delegate system on Ekofisk and later to the introduction of the WEA,” says researcher Trude Meland at the Norwegian Petroleum Museum.
Immediately after the accident, the Ministry of Industry ordered operator Phillips Petroleum to let the workforce elect safety delegates.
A safety and environmental committee was also established, and became a forerunner of today’s working environment committee (AMU) at the operator.
“The accident showed that a new regulatory regime was required,” Meland explains. “The companies couldn’t police themselves.
“Naturally, the American executives in Phillips found the order to introduce safety delegates very strange. Was an employee to be allowed to halt production, they wondered.
“At the same time, the companies were pretty geared up at this time to satisfy the demands set by the Norwegian authorities, so the system was introduced.”
Read more: Tripartite collaboration explained
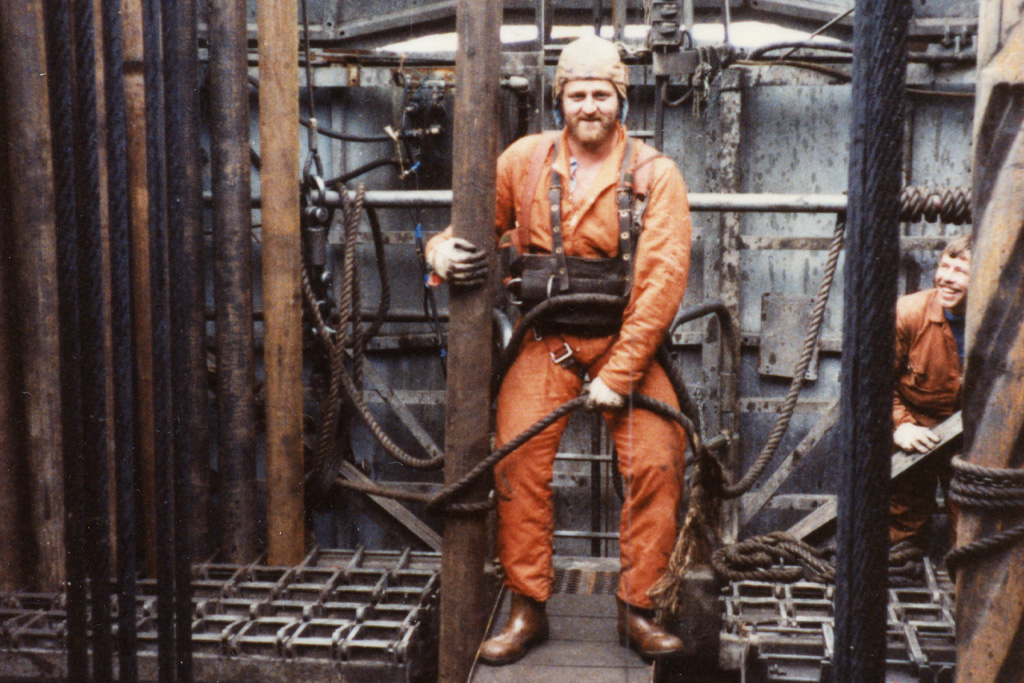
Inquiry
Two weeks after the Alpha accident, a commission of inquiry was appointed with director general Kåre Halden at the Ministry of Local Government and Labour as its chair.
Asked to assess if parts of the WEA, then under preparation, should also apply on the NCS, the commission gave this its support when it reported in the summer of 1976. With some exceptions, the Act was extended to fixed facilities from 24 July 1977.
“That was the great dividing line,” says Meland. “The WEA represented a big step forward for Norwegian workers, and particularly for personnel on the NCS.”
The Act demanded a fully acceptable working environment. It covered such matters as the duties of employers and employees, worker participation, working hours and job security.
Codetermination
The WEA secured codetermination for employees by making elected safety delegates and an AMU – with representatives of both management and workers – obligatory. Management was required to collaborate with the delegates.
“It represented a radical shift,” says Meland. “The workers were now to occupy centre stage. Workplaces should be tailored to employees, who had the right to be consulted.
“This was disquieting for employers on the NCS – but not so radical in mainland Norway, where a long tradition of ‘tripartite’ collaboration prevailed between employers, unions and government, and where trust between management and workers was greater.”
Norwegianisation
Meland believes that the extension of the WEA to the NCS must also be seen in light of the Norwegianisation policy which set its stamp on the oil sector for much of the 1970s.
“This was part of a process which took place at all levels during that period,” she says, and notes that Norwegianisation was about the ownership of resources.
It also covered prioritisation of domestic companies, building up national expertise, getting locals into senior jobs and extending the country’s labour relations system offshore.
“The WEA played its part in making the continental shelf Norwegian,” Meland says. “It was about ensuring that offshore workers were on an equal footing with their counterparts on land. That was key.”
Milestones for safety in the 70s:
1972: Storting (parliament) approves the creation of the NPD and Statoil.
1975: Fire in riser on Ekofisk 2/4 Alpha facility. Three people die. Political turning point for increased commitment to offshore safety.
1976: NPD rejects Mobil/Statoil plan for Statfjord B and calls for quarters to be moved. Named “the most expensive letter in Norwegian history”.
1977: Oil blowout on Ekofisk 2/4 Bravo. This incident prompts a thorough review and evaluation of the safety regime.
1977: WEA extended to fixed facilities on the NCS.
1978: Storting decides that the NPD will report to two ministries – Local Government and Labour for safety, and Industry (now Petroleum and Energy) for resource management.
Platforms only
However, the WEA only applied to fixed facilities offshore – the platforms. Work on mobile units – the rigs – was regarded as maritime activity and remained subject to the Seamen’s Act.
The differences between fixed and mobile facilities were great and persisted for many years.
“They were two completely different worlds,” observes Meland. “Norwegians secured key roles on the fixed units from an early stage, which coloured the working environment and culture there.
“That in turn influenced the introduction of the WEA, which was accepted very quickly and with little conflict. The whole Norwegianisation process had then been under way for some time.
“On the rigs, American drilling contractors dominated and it took a long time before the leadership became Norwegian. Drilling wasn’t an easy occupation for nationals to enter. Even though the plan was to train them up, the first Norwegian drillers were not in place until the early 1980s.”
American management remained stronger on the rigs for much longer, she says.
“Mobile units were considered part of the fleet in foreign service.
“The WEA wasn’t introduced, working hours differed from the platforms and pay was lower. An offshore supplement negotiated in 1981 didn’t benefit rig workers, for example.”
Regulatory responsibility for mobile units was transferred from the Norwegian Maritime Directorate to the NPD in 1985, while the WEA was extended to them in 1992.
Get the hard copy
Do you want to receive the special edition of "Dialogue" for free? Send an e-mail to dialog@ptil.no.
Foundations
Regulators, unions, the internal control principle, allocation of responsibility, the WEA, tripartite collaboration and trust – the foundations of today’s safety system were developed in 1975-82, says Meland.
“The Alexander L Kielland disaster in 1980 manifested the importance of safety work, but much was under way or in place before that,” she adds.
Research needed
She believes that more research is needed on factors related to the introduction of the WEA and its significance. “Many books have been written on Norway’s oil history, but little research done.
“Too few questions have been asked. We ought to know more, for example, about how downturns and the business cycle have affected the working environment and safety.
“That’s also important for understanding today’s position and challenges. Trust and tripartite collaboration come under pressure in hard times. But undermining trust is dangerous. It’s among the most important things which need protecting.”
A good working environment has a positive effect on health, motivation and sickness absence among employees, as well as on productivity and profitability. It also cuts costs for society.
Roar Høydal, discipline leader, PSA
Fundamental
The current version of the WEA came into force on 1 January 2006, building on the 1977 Act and earlier industrial safety legislation.
“It’s fundamental to working life in Norway, including in the petroleum industry,” says Roar Høydal, discipline leader for occupational health and safety at the PSA.
The Act can be regarded as a framework and a recipe book, setting goals, requirements and rules which ensure a positive working environment for individuals, enterprises and society.
It has been developed to provide secure terms of employment and equal treatment in the labour market – and to protect against physical and mental harm.
Another purpose is to ensure that the working day is meaningful and promotes health, and to contribute to a more inclusive workplace.
“The WEA regulates basic requirements for the working environment and specifies requirements for systematic efforts on HSE by the companies,” says Høydal.
“It establishes the rights and duties of both employers and employees, points out the direction of travel and sets priorities.”
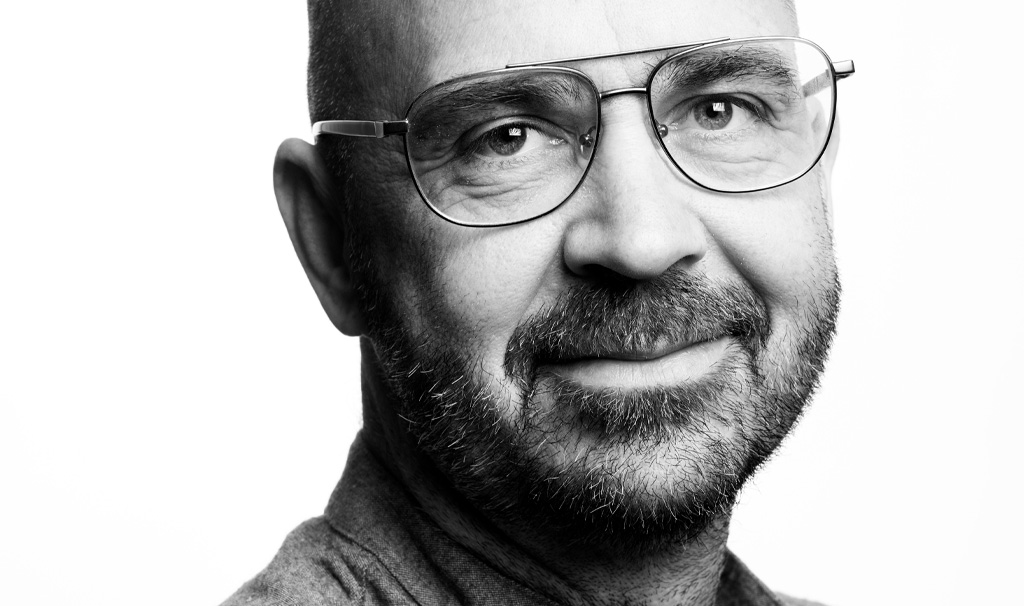
Continuous
A key aspect of the WEA is its emphasis that efforts to improve the working environment are a continuous process, where active use must be made of employee experience.
Worker participation is regarded as so important that employers are subject to legal requirements on both the content of and the process for such involvement.
More detailed
A number of regulations have been introduced to amplify the requirements of the Act by providing more detailed provisions.
“We supervise compliance by companies in the petroleum sector with the requirements of the WEA and associated regulations,” explains Høydal.
“In addition, we have our own specific regulations for the oil and gas sector which supplement the Act.
“Our assessment is that most companies work systematically with the working environment, although areas requiring improvement always exist.”
He adds that it pays to have a good working environment. “This has a positive effect on health, motivation and sickness absence among employees, as well as on productivity and profitability. It also cuts costs for society.
“The key to success is to work preventively, systematically and on the basis of knowledge.”
Read more: Ekofisk - a cradle for safety progress